Air Set / No Bake and Green Sand Mold Aluminum Sand Casting
The Sand Mold Department in our aluminum sand foundry consists of automated molding, Roto-lift, squeezer, and an air set line with our new Kloster air set molding machine, along with a Hunter 20, and a Hunter 32 line in our Fairfield Iowa molding location. High quality sand molds, with the dimensional characteristics and surface finish that you require, begin with closely monitored sand controls. Our computer controlled sand preparation and distribution system maintains proper moisture and consistency of our molding sand using in-line digital sensors.
Air set or No Bake Sand Molding Process
Our Aluminum Foundry’s Air Set, or sometimes called No Bake, sand mold making process uses a dry sand and a fast curing chemical mixture to produce the sand molds. In this process the patterns are filled with the air set sand mixture and compressed, making the cope and drag of the expendable sand mold for the aluminum casting. The air set process allows for tighter dimensional accuracy and also offers better surface finishes. These sand molds can also be internally cored using our shell sand cores, cold box sand cores, and oil sand cores from our Sand Core Department to produce highly complex aluminum castings. This allows our aluminum sand foundry to meet all your large and small aluminum casting needs!
Green Sand Molding Process
In our aluminum sand foundry's green sand molding process the patterns to make our sand molds are filled with the wet sand mixture, which is bonded by clay, and compressed making the cope and drag of the expendable sand mold. This sand mold can then be sent to our Aluminum Melting & Casting Department and cast or it can also be internally cored using our shell sand cores, cold box sand cores, and oil sand cores from our Sand Core Department.
In 2014, ACC installed a new green sand system that increased our capacity, as well as the sand quality. The project included a state-of-the-art sand mixer, and the most advanced sand measurement system available for a green sand aluminum foundry. Every batch of sand is measured for
compactability, green compression strength, and moisture content. This information
is fed back into the control system, where it automatically compensates for any
variability. This means that our customer gets a consistent quality of casting surface
finish and cosmetics.
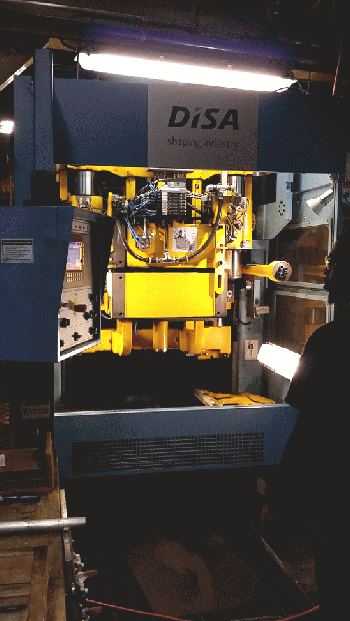
In 2015, ACC installed a new DISA Match flaskless molding machine. The DISA
provides unbeatable mold speed of 150 molds per hour, along with optimum output
of precision castings (minimum mismatch of less than .010”). A Quick Matchplate
Changer (QMC) allows for fast pattern change to accommodate shorter runs.
The DISA technology makes our green sand aluminum foundry exceptionally competitive whether the lot size is
50 or 50,000 pieces. Our DISA Match runs a 20” x 24” plate size, with a 8”/8”
cope and drag height. Aluminum Castings Company's quality and cost-competitiveness is unmatched!
In November of 2018 ACC purchased the operating assets of Alcast Company Midwest Works (formerly FALCO) in Fairfield Iowa to further expand our green sand molding capabilities. Equipment in the ACC Fairfield location includes both a Hunter 20 and Hunter 32 line which has further increased ACC's capabilities allowing us to produce larger green sand aluminum castings.